If you ‘re here, odds are you already know what a baseball mitt is; however, a reminder doesn’t hurt. Baseball gloves or mitts are used by players when they are in a defensive position.
Baseball mitts help players to catch the ball and it is a lot easier than with the bare hand. But in order to know how baseball mitts are made, you must know which materials are used in the process. Let’s find out.
Knowing the materials for baseball mitts
All baseball mitts are made from different types of leather, depending on the position the player would play and of course the manufacturers which create them.
These types are listed as four major materials which are, full grain leather, kip skin, premium steer hide, and cowhide.
Being the last one the most used in the baseball industry because of its excellent performance, its weigh and time to break in.
All four types have an advantage which makes them different from each one, like the premium steer hide and the full grain leather are made to last longer than other leathers are tougher and more durable than others.
On the other hand, kip skin types are the lightest of all, helping the infielders to transfer the ball faster to the hand.
Before the manufacturing process
The first thing you need to know is that the process begins before cowhides reach the factory. All hides must be already cured and tanned before the cutting procedure begins.
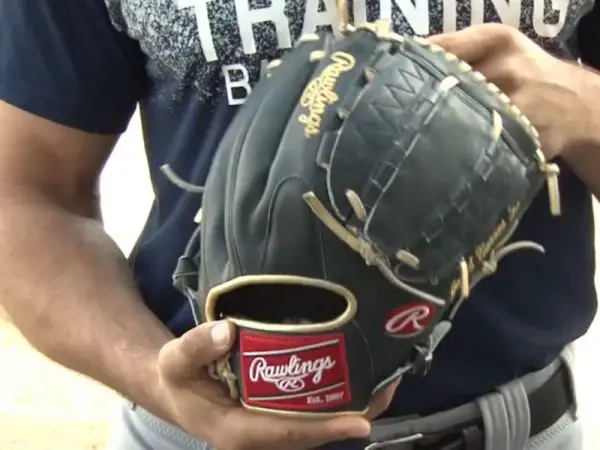
But what is ‘cured and tanned’?
The curing process is where all the bacteria in the leather are killed by salting or drying. After that, leather goes through a chemical treatment called tanning, which gives leather more durability and flexibility, preventing the cowhide to dry in shorter periods of time.
How baseball mitts are made?
The first step in the manufacturing process is die-cut. Cowhides (cured and tanned) are placed into a machine that will cut it in four pieces, the shell, pad, web, and lining.
Once the leather is cut, the shell piece is sewn together from inside-out and then is heated (wetted or steamed) in order to gain the flexibility to further procedures. After being mulled the lining is introduced by turning the shell right-side.
Most manufacturers print their brand before the die-cutting process and others right after the glove gains its hand-shaped by introducing the shell already turned into a device that generates heat and shapes the glove.
The first split in the process begins now as the pad will be introduced. Normal padding for baseball gloves has two layers of leather (stitched together), but as catchers need extra padding to protect their hands, catchers’ mitts are made with 5 layers of leather.
The only plastic material that gloves have is inserted after the padding. This plastic reinforcement goes from the thumb to the little finger to protect fingers from being bent.
Sewing and padding
Meanwhile, people are sewing and padding the shell and lining, others are making the most significant feature of baseball mitts, the web. Right now there are around 8 types of baseball webs, a basket web, trapeze web, modified trap web, H/dual post, I webs, single post web, double post web, and two-piece web.
Each type is for a specific position and purpose, you as a baseball player will soon figure it out which one is best for you and your fielding skills.
So, depending on the design, the web is laced with the shell before the finals stitching is made.
Finally, the last lacing process begins, from closing the glove to strengthen the web-shell union. Non-leather materials such as nylon or other synthetic material are used in this stage of the process.
The estimated time for this process is marked by the web and positions types, for isn’t the same stitching an outfielder glove or a catchers’ mitt.
Remember the hand-shaping device that produced heat? Well, gloves are placed there once more to adjust any shaping problems.
Finals Thoughts
Maybe you would never realize how much work is placed in order to make a single mitt, now that you know everything is done, perhaps you would appreciate more every design and its prices.
Manufacturers still keep trying to create a lighter and most durable glove made with cheaper materials; we hope with all the technological advances they achieve it someday.
Also, remember that professional players with all the money they make can request a special design for them, or the manufacturer would make it for them for free in order to gain publicity.
Looking for more?
If you would like to read more, then we have hand picked some of our most popular pieces.
Information:
How baseball batting average is calculated?
Why are baseball cards valuable?
How baseball players get out of a slump
Equipment & Apparel:
Easton MAKO Youth Baseball Bat Review
Rawlings Prodigy BBCOR review
Best Baseball Glove for 10 Year Old Boy